Overcoming the skilled-worker shortage with robots
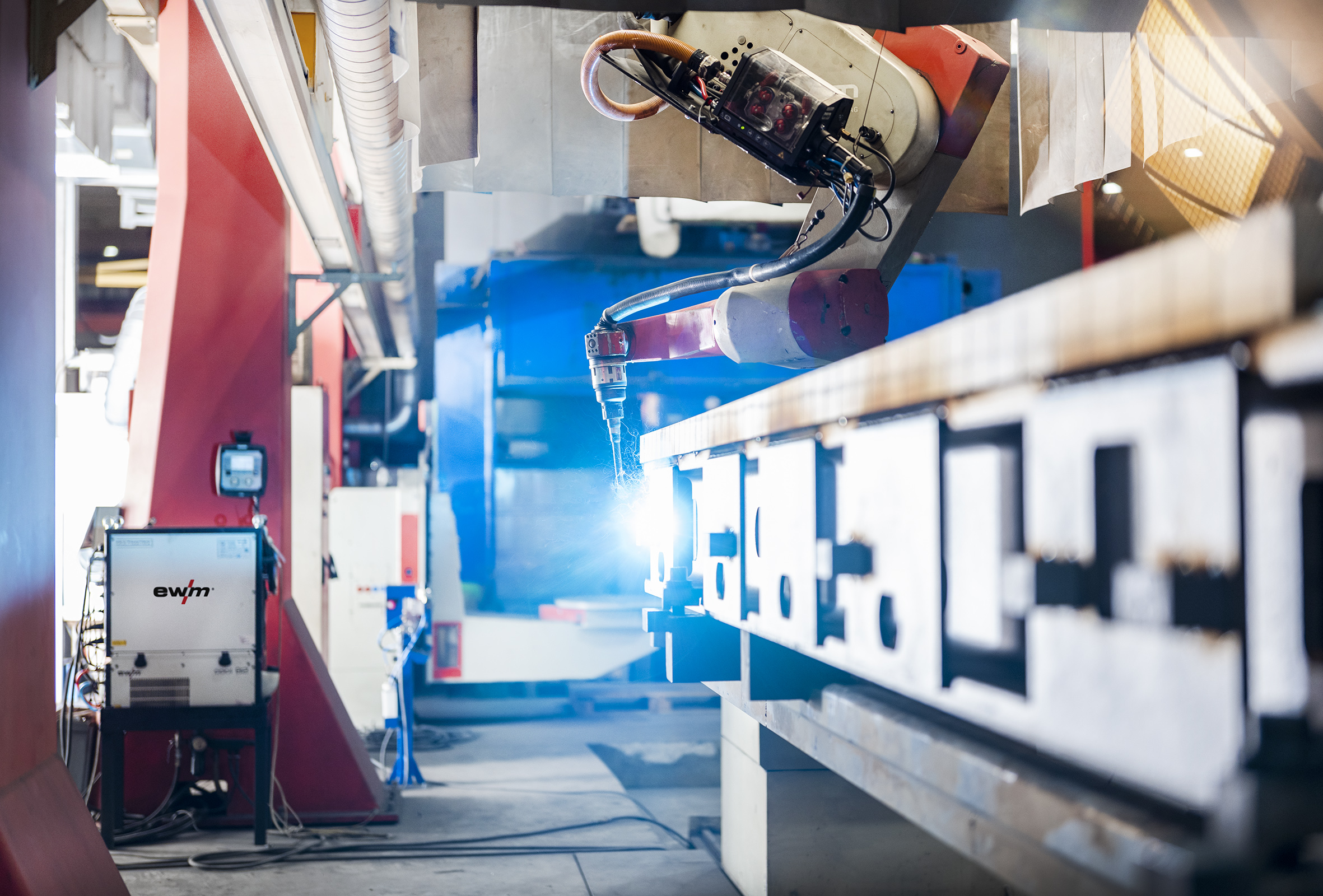
Overcoming the skilled-worker shortage with robots
Automated welding: A host of hurdles on the path to success
In the production process, welding is among the most complex of procedures, and it’s becoming harder and harder to find suitable personnel for the job. Can this problem be solved by automating processes? Can (and should) robotic “colleagues” replace experienced welders? The automation of manual welding is a complex, multi-step process.
Welding and joining technology companies are struggling to find suitable skilled workers these days. Many companies are confronted with a dilemma: a lack of welding specialists and increasing labour costs on the one hand, and on the other, increasing requirements in terms of the quality, flexibility and efficiency of welding processes. This is why companies are increasingly relying on the automation of processes and the use of robots. What used to be commonplace primarily in the automotive industry and large-scale production in past decades is also becoming increasingly important to small and medium businesses in a wide variety of industries. This is because automated welding processes are no longer only economically viable for large corporations. Automation promises completely precise repeatability with consistent weld seam quality, process reliability and increased productivity thanks to minimal set-up and auxiliary process times.
Basic requirements for the automated process
If welding processes are to be automated, there’s more to do beforehand than just determine which components will be produced and what relevant geometries need to be complied with. Specifications about the lot size, tolerances and the desired welding procedures are also important. “It is often essential to first gain an understanding of the process. A robot can’t compensate for a change in position, but a welder certainly can,” remarked Max Lautenbach, Acting Application Engineering/Automation Manager at EWM GmbH. “This being the case, the welding equipment has to be just right, and this usually involves greater effort.” Along with automation come changes to all the processes involved. Processes both upstream and downstream of the welding cell must also be adapted. For example, a sufficient number of components from preproduction must be available so the system can run at optimal capacity. There are also greater requirements in terms of the precision of the components. Welded parts then need to be transported away and stored at the right time so as to avoid a process bottleneck. Personnel available on site also need to be taken into account. “Completely untrained employees can’t operate a robot system,” says Andreas Euen, Managing Director of EWM-EUEN GmbH. “Robots reduce the overall need for personnel, but employees who know how to program a welding cell are needed on site in order to automate processes.”
Cobot versus welding cell
Collaborating robots (cobots) are trendy, and they’re increasingly being used in the welding technology field as well. The big advantage lies in straightforward system operation. A cobot can easily be trained on site and then repeat the processes it has been shown. Complex programming isn’t required, but teaching in should be carried out by specialist staff. Cobots boast a good price-to-performance ratio, which also makes them suitable for use by smaller companies. The aspect of safety also has to be taken into account here, as the welding process comes along with a multitude of risks – from potential welding sparks, to the generation of hazardous radiation, to electrical hazards and the creation of harmful substances. This means that “hand-in-hand” work with a cobot with a burning arc is hardly possible at all. Compact welding cells, which are also cost-efficient, are attractive to smaller companies. XQbot welding cells from EWM, for example, are a good introduction to automation. The driving force of these cells is the CRX robot from FANUC, which is comparable to an industrial robot with regard to accuracy, precise repeatability and stability. This means that small and very small series can be produced without extensive programming effort, with the operator enjoying maximum protection.
Analysing welding processes down to the smallest detail
If components are imprecise or equipment is unstable, additional measurement traversals are often required to ensure exact positioning. This quickly makes the entire process inefficient. If done manually, however, the welder can immediately respond to changes and notice if the sheet metal is moving during welding, for example. In this case, the robot would simply weld a few millimetres next to the desired position. This means that the weld seam is in the wrong location and the component can’t be used. This is why the welding process should be analysed down to the smallest detail beforehand. Does it even make sense to switch over to automated production? Do so many changes have to be made that the idea wouldn’t be economically worthwhile? Suppliers have to support potential users with competent advice during the planning, installation and commissioning of welding cells. This includes a comprehensive initial consultation, concept creation and a feasibility analysis. The component to be welded must be thoroughly examined and evaluated. Prior to operation-ready set-up on site, initial sample welding should also be carried out on the supplier’s robot welding systems. Here, the customer receives a comprehensive introduction to programming, and can check the welding process and results. Once the right system has been selected, the customer receives comprehensive training in operation, and professional support is also provided even after the system has been installed. “The most crucial factor isn’t the robot, but rather the welding technology in use. To achieve the best possible results, suppliers need to provide the necessary professional competence,” says Wolfgang Kumpf, Head of In-House Sales at EWM.
Practical example: automation in chassis production
EWM-EUEN GmbH implemented an automation solution with a welding robot for a lorry trailer manufacturer. The skid trailers and roll-out trailers are always manufactured from the same assemblies. New clamping equipment was intended to make work on the 7-metre-long and 2.4-metre-wide trailers easier for the welders. EWM-EUEN GmbH implemented a gantry system with nine axes. A Phoenix puls welding machine from EWM is used here. The skid trailers and roll-out trailers are each produced in two separate working areas. Whilst the robot is welding in one section, the other can already be loaded. Welders insert the longitudinal girders and welded assemblies, tack weld them and then weld extra-short seams straight away. When the robot is finished welding in one booth, it moves into the second booth and continues welding there. The finished chassis is removed, and the cell is loaded again. While the timing of the robot was initially a major challenge for welders, the workflows are now running smoothly. As the entire welding process is based on taught-in curves, there can’t be any major deviations among the individual components – this presents a major challenge during part preparation. The thermal expansion of components also had to be taken into account. This is why it took a few passes for the welders to program the components perfectly to ensure optimal contact with the weld seam at all times. Productivity increased enormously as a result of chassis production automation. The manufacturer was able to nearly double its production with reduced manpower. 300 weld seams can now be created within 90 minutes. Thanks to the high quality of the weld seams and the minimal weld spatter, subsequent reworking was reduced by 30 percent.
Conclusion: When automating welding processes, it’s essential to view the system holistically. The focus should be on welding, not the movement of the robot. This can’t replace trained professionals, but it can relieve the burden on them when it comes to carrying out monotonous and exhausting work. This frees them up for activities which create more value. This means that a successful transition to automated welding processes during skilled-worker shortages can be a sensible solution which measurably increases productivity and competitiveness.