Sustainable welding
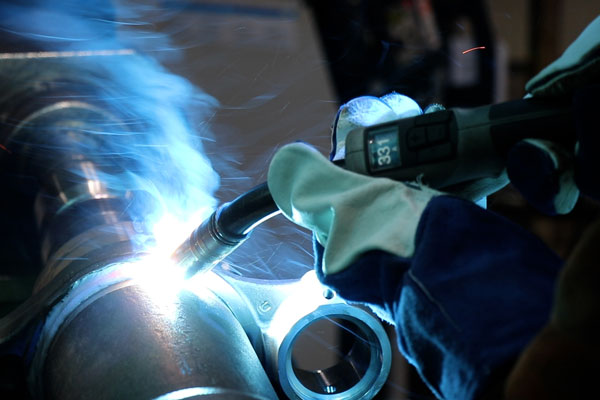
Sustainable welding
How resources can be conserved while reducing costs
At industrial companies, both sustainability and climate protection are increasing in importance all the time, but sustainable production doesn’t necessarily have to come with increased costs. With their BlueEvolution® initiative, EWM are showing how economic viability and ecology can be reconciled in welding. Resource-conserving inverter technology and energy-reducing joining processes not only improve ecological balance, but also considerably increase the efficiency of welding processes.
In order to produce sustainably, companies have to balance social, ecological and economic matters in a reasonable way. This applies to welding processes, too. A lot of adjustments can be made when machines are to be manufactured and used – and processes carried out – in an environmentally friendly way. The use of inverter technology, for example, results in a considerable reduction in the use of raw materials while at the same time increasing efficiency. Transductor- and magnetic-amplifier-based power sources, and other machines with a primary transformer, lose more energy than modern inverters, which boast greater efficiency and lower energy requirements. A study conducted by EWM showed that the amount of current consumed when using the Phoenix XQ 400 with inverter technology dropped by 3,643 kWh annually as compared to the step switch controlled WEGA 400 power source. This involved welding in the area of the spray arc with a filler wire with a diameter of 1.2 mm. Based on the energy prices at the time of measurement, the electricity costs were reduced by around 730 euros. Inverters aren’t just more efficient, but are also several times more compact and lightweight than step switch controlled power sources. For example, the transformer of a step switch controlled welding machine rated at 20 kW weighs around 100 kg, whereas the transformer of the Titan XQ 350 puls from EWM with the same power rating comes in at a mere 5 kg. Less material is also required to manufacture inverter power sources, and thus smaller amounts of copper, aluminium and steel are consumed. The use of inverter power sources ensures a reduction in CO2 emissions as well. This is already the case during manufacturing. If 10,000 inverter power sources are built annually, this represents a reduction of more than 1,100 metric tonnes of CO2 in comparison to the construction of power sources using conventional technology.
Advantages of inverter technology
When using step switch controlled welding machines, the user has next to no influence on welding process control. With inverter power sources, on the other hand, it’s possible to implement waveform-controlled welding processes which considerably reduce energy and welding fume emissions. For example, the forceArc® XQ and forceArc® puls XQ welding processes from EWM enable considerably smaller included angles in comparison to conventional welding processes. This means that fewer weld runs are required. The reduction in weld seam volume affects both welding preparation time and weld time. The heat-minimised, directionally stable and powerful arc with deep penetration in the upper power range also allows for a reduction in welding consumables. In addition, less finishing work is required thanks to minimal spatter. Ultimately, the user benefits from a reduction in the amount of energy, material, time and money required. In comparison to conventional welding machines with a standard spray arc, those with forceArc® XQ can actually reduce overall costs by up to 60%.
Significant reduction in emissions
Heat-reducing processes like forceArc®, forceArc puls® and coldArc® reduce the emission of harmful welding fume particles, which protects both people and the environment. “In a study, Dresden University of Technology proved that emissions can be reduced by up to 40% by using forceArc® instead of welding with a conventional spray arc”, says Dipl.-Wirtsch.-Ing. Boyan Ivanov, Technical Sales Manager at EWM. “More of the welding fumes are deposited on the surface of the workpiece, so these emissions aren’t released into the environment. As a result, this procedure ensures improved working and environmental conditions.” In another study, this time by RWTH Aachen University, the effect of the forceArc® puls XQ process was confirmed. When welding high-alloy CrNi steels, the emissions rate at a wire feed speed of 13 m/min dropped 4.5 times as compared to a welding process with a conventional pulsed arc. The advantages of the forceArc® puls XQ process become especially clear at higher power levels. In comparison to the standard welding procedure with a short arc, the coldArc® process also results in considerably lower emissions values. Lots of welding fumes are always created when the welding consumable contacts the workpiece and a short circuit occurs. “We’re able to control the short-circuit resolution very well with the inverter”, said Ivanov. “The short circuit then occurs in a controlled way, and welding fumes are minimised. On top of that, hardly any spatter is created.
Reducing gas consumption over the long term and ensuring reliable processes
It’s often the case that the gas volume for a welding process is set incorrectly – that is, excessively high. This results in increased gas costs and a drop in weld seam quality. Pores are formed, which can lead to porous weld seams. Spatter is also generated, which then has to be removed through expensive, time-consuming finishing work. Thanks to digital gas control in the wire feeder, this can be avoided. Digital control ensures continual gas flow. The shielding gas can be actively controlled. If something changes in the gas supply, the machine automatically adjusts the volume and issues an error message, if necessary, if the limits set in advance are exceeded or undershot. This ensures a stable, reliable process and prevents excessive gas consumption. Thanks to the soft opening and closing of the electrical valve, turbulence isn’t created when the arc is ignited. The laminar gas supply of EWM welding torches reduces the amount of shielding gas used by up to 25%.
Energy consumption and CO2 emissions values always in view
However, sustainable welding also means that the entire process has to be checked and monitored. If improvements are to be made in the area of environmental protection, you have to know what the resource and energy consumption values are in the first place. They’re easy to determine with the ewm Xnet welding management system for Welding 4.0. All welding machines at the factory are networked with one another. This means that welding data, consumption and costs can be displayed and managed for different components. Gas, energy and material consumption values are continuously recorded. This makes it possible to identify potential for savings straight away. You’re notified of necessary maintenance work in a timely manner so the service life of the systems and machines can be optimised. As a result, the system ensures top quality, enables process improvements and simplifies documentation. “Xnet calculates the energy consumption for each welding machine – per day or per job – as needed”, explains Ivanov. “With our new version, we’ve made calculation of emissions values possible at the same time. This makes it easy to determine whether the CO2 emissions are within the specified window or if they’re too high and need to be reduced accordingly.” With ewm Xnet, the company thereby gets an important monitoring tool in a market where the number of CO2 certificates available is continuing to drop as their price increases. The rules for EU emissions trading are already being tightened in order to motivate greenhouse gas producers to implement further climate-protection measures. CO2 certificates are an important part of the overall balance of a company. With their welding management software, EWM provide an important component for improving the quality of welding processes, reducing costs and emissions and, ultimately, increasing productivity in conjunction with an increase in sustainability.
Conclusion: Sustainable welding pays off
“We were one of the first welding machine manufacturers to get started in this area with our BlueEvolution sustainability initiative”, says Boyan Ivanov. “This allows us to demonstrate that the required raw materials and energy can be reduced thanks to modern technology and innovative welding processes. This contributes to climate protection and sustainability, while at the same time resulting in a noticeable reduction in costs.” Welding times can be decreased, which in turn increases productivity. Furthermore, considerable amounts of emissions can be slashed, which not only improves the ecological balance, but workplace conditions as well. EWM technology also supports future-oriented designs and the use of new materials here. For example, the trend in crane building and wind turbine construction is towards the use of thin, yet extremely strong, materials. In order to weld these sensitive materials in an optimal way, you need procedures which are specially oriented towards the task, corresponding inverter technology and comprehensive expertise. After all, a weld seam can only be perfect if the welding process conserves energy and resources.