Setting welding parameters all in one place
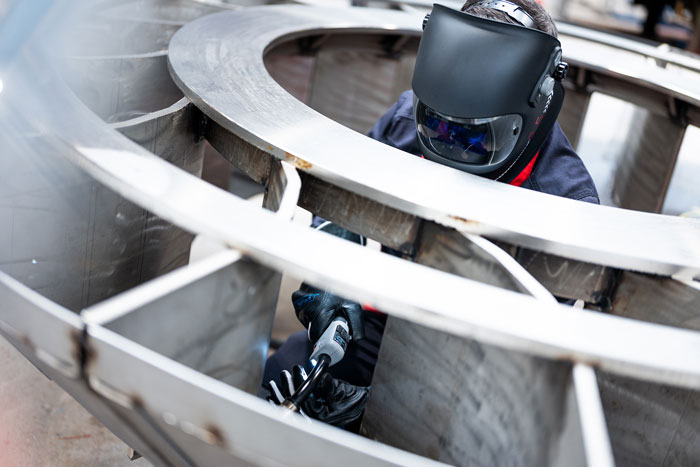
Setting welding parameters all in one place
Every function accessible on the welding torch
Welded constructions as big as houses are typical at Ebner, the specialist for heat treatment technology and industrial furnace construction based in Leonding, Austria. For these kinds of tasks, the mobility and flexibility of the welding technology play a major role, and EWM’s new RD X3 PM welding torch meets these welders’ requirements, as all parameter settings can be implemented directly via the integrated display. This means it is no longer necessary to walk to and from the welding machine, making welding much more productive.
Having a head for heights is virtually part of the job description for welders at Ebner, with the weld seams often situated up to five meters above the ground. It goes without saying that the welders are provided with ample safety equipment. Once the welder gets up off the ground, they want to be welding, not climbing.
Every function accessible on the welding torch
“Being able to change parameters on the torch itself, without restriction” is one of the main advantages of a PM welding torch, according to Christian Gruber, Ebner’s Welding Supervisor. This function makes the welder’s job significantly easier, especially with hard-to-reach components. The welder can make changes to the machine control from their welding position. The torch’s optimised ergonomics, including reduced weight and balanced-out design, allow for effortless welding. The integrated LED light illuminates dark working areas.
50-metre action radius
The action radius between the EWM Titan XQ puls power source and the welding torch can reach up to 50 metres thanks to the intermediate hose packages and the Drive XQ wire feeder. The integrated eFeed mechanism allows it to feed the wire precisely using four wire feed rolls which are driven synchronously. Roll change takes place without the need for tools. The Titan XQ puls can even be fitted with two wire feeders, each of which comes with a separate hose package and is connected to its own welding torch. It is also possible to connect two different shielding gas cylinders. The user can simply switch to the other welding torch to change the welding wires for individual layers of the seam. The relevant welding parameters are stored in the control and can be selected on the torch at the press of a button.
All in: one for all
Titan XQ puls is a new MIG/MAG multi-process welding machine which can be digitally networked on a broad scale, making it ideally equipped for Industry 4.0. All of the innovative welding processes are optimised by the modern RCC inverter technology and, thanks to the new control, can be selected directly on every welding machine, where they are made available as standard. This means that the right welding process is available for every task and can be selected and activated directly on the torch. Due to the wide variety of materials and applications they deal with, Ebner’s welders use almost all of the innovative welding processes, which allows them to carry out a huge range of applications. Since every innovative welding process was specially developed for a specific application, these processes are increasingly replacing standard ones.
MIG not WIG
At Ebner, some of the chromiumnickel materials were welded using Tungsten Inert Gas (TIG) until the welders familiarised themselves with the new innovative forceArc puls welding process on the Titan XQ puls. Since then, chromium-nickel materials have been welded less and less with TIG and increasingly using the MIG (metal welding with inert gases) and particularly the MAG (metal welding with active gases) shielding gas welding processes. With the forceArc puls welding process, the quality of the MIG weld seam is comparable to that of a TIG seam, but it can be done at significantly greater speed, making it much more effective when producing long weld seams. The switch from TIG to MIG also benefits the company in terms of welder qualifications: “Welding with MIG only requires passing two or three exams, compared to seven needed for TIG welding.” According to Gruber, this makes it easier for welders to complete training and gain qualifications.”
Consumable: contact tip
The contact tip may only be a small component, but it is fundamental in the welding process and the achievement of good welding results. “Consumables usage has decreased significantly and this is especially true of contact tips,” says Gruber about his experiences with the welding torches. Reduced consumables costs are one thing, but what’s much more important is the avoidance of follow-up costs thanks to the longer service life of the contact tips. The contact tip’s replacement times are reduced, creating more time for welding. The long service life and consistent wire feeding also maintain the weld seam quality at a steady, high level.
EWM once – EWM forever
The management at Ebner decided four years ago to put technology to the test: welders, maintenance staff and welding coordinators took machines from four prominent welding manufacturers and put them under the microscope. EWM came out on top and Ebner switched over to EWM machines for all of its welding production. The optimisation offered by ewm maXsolution innovation and technology consulting was especially suited to Ebner’s needs. When the time came for Ebner to purchase new welding machines, they were certain that they wanted EWM‘s latest technology: As Gruber sees it, “Our welders should have access to the best machines on the market”. This is why the workstations where welding is carried out continually have been equipped with a Titan XQ puls, as well as the training workshop, where trainees can learn how to use this innovative technology and build up experience. Gruber values this investment enormously.
Date: 12 November 2020
Volume: 6,085 characters including spaces
Figures: 5