Einstellen der Schweißparameter ohne Laufwege
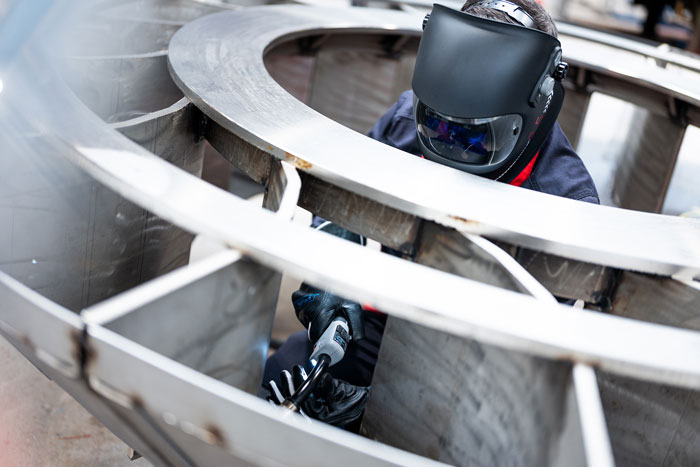
Einstellen der Schweißparameter ohne Laufwege
Alle Funktionalitäten im Brenner
Schweißkonstruktionen in der Größe eines Einfamilienhauses – das sind die typischen Abmessungen bei Ebner, dem Spezialisten für Wärmebehandlungstechnologien und Industrieofenbau aus dem österreichischen Leonding bei Linz. Bei solchen Aufgabenstellungen spielen Mobiliät und Flexibilität in der Schweißtechnologie eine ganz besondere Rolle. Da kommt den Schweißern der neue PM-Brenner RD3X des Schweißgeräteherstellers EWM gerade recht: Sämtliche Parametereinstellungen lassen sich direkt auf dem integrierten Display vornehmen. Die Laufwege zum Schweißgerät entfallen damit – und das Schweißen wird viel produktiver.
Schwindelfrei zu sein gehört bei Ebner fast schon zu den Einstellungsvoraussetzungen als Schweißer. Denn die Schweißnähte befinden sich oft in Höhe von bis zu fünf Metern über dem Fußboden. Selbstverständlich sind die Schweißer gut gesichert. Wenn der Schweißer erst einmal oben ist, möchte er schweißen und nicht klettern.
Alle Funktionalitäten im Brenner
„Die Parameteränderungen direkt am Brenner vorzunehmen – uneingeschränkt“, das sieht Christian Gruber, Supervisor Welding bei Ebner, als einen der Hautpvorteile des PM-Brenners an. Gerade bei unzugänglichen Bauteilen erleichtert diese Funktion die Arbeit enorm: Der Schweißer kann aus seiner Schweißposition heraus Änderungen in der Gerätesteuerung vornehmen. Die optimierte Ergonomie des Brenners mit dem geringeren Gewicht und dem ausbalancierten Design unterstützt ermüdungsfreies Schweißen. Das integrierte LED-Licht leuchtet dunkle Arbeitsbereiche aus.
Aktionsradius 50 Meter
Bis zu 50 Meter kann der Aktionsradius zwischen der Stromquelle Titan XQ puls von EWM und dem Brenner betragen. Das ermöglichen Zwischenschlauchpakete sowie das Drahtvorschubgerät: Drive XQ. Mit seiner integrierten Drahtvorschubeinheit eFeed fördert es den Draht mithilfe von vier synchron angetriebenen Drahtvorschubrollen präzise. Ein Rollenwechsel erfolgt werkzeuglos.
Die Titan XQ puls kann auch mit zwei Drahtvorschubgeräten ausgerüstet sein. Jedes verfügt über ein separates Schlauchpaket und ist jeweils mit einem eigenen Schweißbrenner verbunden. Ebenso können zwei unterschiedliche Gasflaschen angeschlossen werden. Um die Schweißdrähte für einzelne Lagen der Naht zu wechseln, nimmt der Bediener einfach den anderen Brenner. Die entsprechenden Schweißparameter sind in der Steuerung hinterlegt und werden auf Knopfdruck direkt am Brenner abgerufen.
all-in: Eines für alles
Titan XQ puls ist ein neues MIG/MAG-Multiprozessschweißgerät, das sich umfassend digital vernetzen lässt und damit Industrie-4.0-tauglich ist. Sämtliche innovativen Schweißprozesse sind durch die moderne RCC-Invertertechnologie optimiert, dank der neuen Steuerung direkt anwählbar und serienmäßig auf jedem Schweißgerät verfügbar. So ist für jede Schweißaufgabe der richtige Schweißprozess vorhanden – und kann direkt am Brenner aufgerufen und umgeschaltet werden.
Aufgrund der großen Materialvielfalt und der hohen Anwendungsbreite setzen die Schweißer von Ebner fast jeden der innovativen Schweißprozesse ein und können damit ein riesiges Anwendungsspektrum abdecken. Da jeder innovative Schweißprozess speziell für eine bestimmte Anwendung entwickelt wurde, ersetzen diese Prozesse auch immer mehr die Standardverfahren.
MIG statt WIG
Bei Ebner wurde ein Teil der Chrom-Nickel-Werkstoffe mit Wolfram Inert Gas (WIG) geschweißt – bis die Schweißer bei der Titan XQ puls den neuen innovativen Schweißprozess forceArc puls kennenlernten. Seitdem werden immer mehr der Chrom-Nickel-Werkstoffe nicht mehr mit WIG, sondern mit den Schutzgasschweißverfahren MIG (Metallschweißen mit inerten Gasen) und vor allem mit MAG (Metallschweißen mit aktiven Gasen) geschweißt – Tendenz steigend. Unter dem Schweißprozess forceArc puls ist die Nahtqualität der MIG-Schweißnaht mit der Qualität der WIG-Naht vergleichbar, die Geschwindigkeit ist es nicht: Sie ist deutlich höher und damit für die Herstellung der langen Schweißnähte deutlich effektiver.
Auch für die Qualifizierung der Schweißer ist die Umstellung von WIG auf MIG ein deutlicher Vorteil für das Unternehmen: „Wenn wir mit MIG schweißen, müssen wir gegenüber WIG nicht mehr sieben Prüfungen verlängern, sondern nur noch zwei oder drei.“ Das vereinfacht nach Aussage von Gruber auch die Ausbildung und die Qualifizierung.
Verschleißteil Stromdüse
Auch wenn die Stromdüse nur ein kleines Bauteil ist, so ist sie für das Schweißen selbst und für die Schweißergebnisse fundamental. „Besonders bei der Stromdüse ist der Verschleißteilverbrauch enorm zurückgegangen“, beschreibt Gruber seine Erfahrungen mit den PM-Funktionsbrennern. Dass dadurch die Kosten für die Verschleißteile sinken, ist das eine. Viel wesentlicher aber sind die Folgekosten, die durch die längere Lebensdauer der Stromdüsen gar nicht erst entstehen: Die Wechselzeiten der Stromdüse sind reduziert und können für das Schweißen eingesetzt werden. Durch die lange Lebensdauer und den konstanten Drahtvorschub ist auch die Schweißnahtqualität gleichbleibend hoch.
Einmal EWM – immer EWM
Nur mit den besten Schweißgeräten lassen sich auch die besten Ergebnisse erzielen – aus dieser Überzeugung heraus veranstalteten die Verantwortlichen von Ebner vor vier Jahren eine Challenge: Schweißer, Instandhalter und Schweißaufsichtspersonen nahmen die Geräte von vier namhaften Schweißgeräteherstellern genauestens unter die Lupe und prüften sie auf Herz und Nieren. Positiv aufgenommen wurde im Zuge dieses Tests die tatkräftige Unterstützung durch die Anwendungstechniker des EWM-Standorts Österreich. EWM gewann dieses Rennen und Ebner stellte seine gesamte Schweißfertigung auf EWM-Geräte um. Insbesondere die Optimierung im Rahmen der Innovations- und Technologieberatung ewm maXsolution kam den Ansprüchen bei Ebner durchaus entgegen.
Als bei Ebner neue Schweißgeräte angeschafft werden mussten, war der Hersteller sofort definiert: EWM. Dass es die neueste Technologie des Anbieters sein sollte, war auch klar: „Unsere Schweißer sollen mit den besten auf dem Markt verfügbaren Geräten arbeiten können“, so die Ansicht von Gruber. Deshalb sind vor allem die Arbeitsplätze, bei denen kontinuierlich geschweißt werden muss, mit einer Titan XQ puls ausgestattet worden – und die Lehrwerkstatt. Auch dort sollen die Auszubildenden gleich mit der innovativen Technik in Kontakt kommen und ihre Erfahrungen sammeln können. Diese Investition war Gruber ganz besonders wichtig.
Stand: 04. November 2020
Umfang: 6.504 Zeichen inklusive Leerzeichen
Abbildungen: 5