Top quality in continuous use
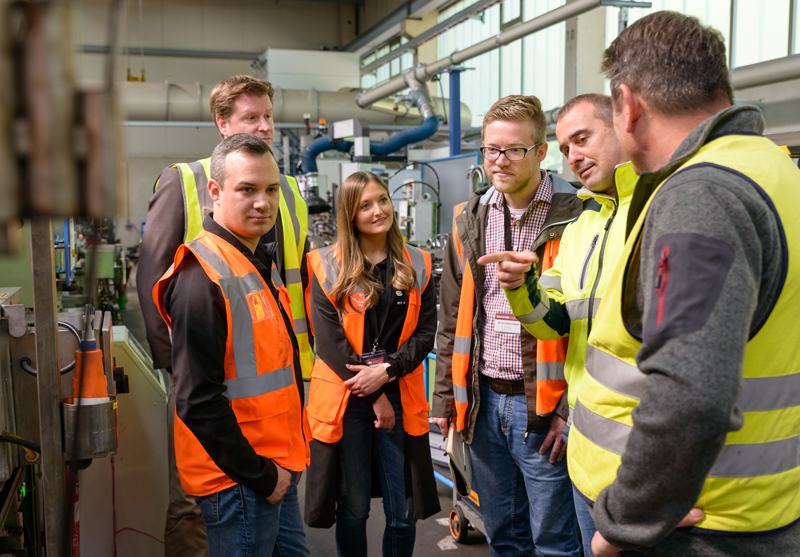
100,000 hours of operation: Schoeller Werk trusts welding machines from EWM
Top quality in continuous use
The family-run Schoeller Werk GmbH & Co. KG is one of the world’s leading manufacturers of longitudinally welded stainless-steel tubes. Schoeller’s customers expect excellent quality products and, in order to fulfil this demand, Schoeller has relied on welding machines from EWM AG for some 25 years. Around 300 machines are currently in operation, including the Tetrix and Tetrix plasma models. The tube manufacturer’s production lines still feature some of the original EWM machines, which have been running smoothly since the mid-1990s. What makes this even more special is the fact that the welding machines run in three-shift and sometimes even four-shift operation around the clock. As a result, they have been in operation for a total of around 100,000 hours – a sign of extreme durability, which is no longer guaranteed in modern times of planned obsolescence.
Founded in 1827 and headquartered in Hellenthal in the Eifel region, Schoeller Werk employs more than 1,000 people in an operating area of 100,000 square metres, making it one of the region’s major employers. Their product portfolio includes TIG, TIG plasma and laser-welded stainless-steel tubes as well as redrawn precision tubes, which they supply in straight manufacturing and fixed lengths and also as coiled tubing. Driven by innovation, Schoeller is always working on the development of its system technology and product portfolio in line with the demands of its customers and the market. The high-quality manufacturing of their products is made possible by modern machinery. Every year, Schoeller produces around 90 million metres of stainless-steel tubes for use in the automotive and manufacturing industries. At Schoeller Werk, customers get everything from a single source – whether it be technical consultation, application-specific product development and tube manufacturing, comprehensive quality checks or custom logistics services.
An EWM customer from the start
This has also been made possible by the company’s long-standing partnership with EWM. Schoeller has been a customer of the German welding technology manufacturer since 1995, and what makes this even more special is the fact that EWM only started manufacturing its own welding machines in 1993. Prior to that, the company manufactured components for the global welding technology market. This means Schoeller Werk has been with us nearly from the very start, when EWM took the leap to becoming a machine manufacturer. In almost 25 years working together, the company has always remained loyal to EWM. “We used to use classic welding rectifier technology. Those were robust, heavy machines with lots of copper and very few setting options: the machine would either supply current or it wouldn’t,” remembers Stefan Fink, Maintenance/Technology Manager at Schoeller. He has been employed there for 34 years and knows the machines inside out. The company worked with the welding institute of the RWTH Aachen University to introduce inverter technology. However, the welding machine manufacturer Schoeller previously worked with didn’t yet have this technology in its portfolio, and so the switch to EWM was made.
Driving innovation together
The collaboration between Schoeller and EWM has always been defined by a relationship of trust, fast response times and reliable service. If there is a change in what is required of the machines, EWM reacts immediately. “EWM also invests a great deal in its own research and development, which allows us to drive innovation together,” Stefan Fink explains. Schoeller has a testing facility where it tries out new EWM technologies. As a result, Schoeller now uses TIG plasma technology, whereas before it only used TIG welding. The collaboration has also proved fruitful in terms of the development of new Schoeller products. The company’s decision to start manufacturing fuel distributor tubes in 2008 was put into practice in collaboration with EWM, and now Schoeller is Europe’s leading producer of these tubes.
Welding machines customised for Schoeller’s needs
The welding machines not only have to assist in the development of new products at Schoeller, but they are also subjected to a high workload in general. The machines in Hellenthal are in operation 24 hours a day, 7 days a week. In addition, the walls of the tubes are becoming thicker, which in turn increases the current load of each individual machine. Therefore, EWM has worked with Schoeller to customise the welding machines according to their own specific requirements. Especially the control, which is responsible for the precise operation of the machines, has various Schoeller specifications. “When we order a welding machine from EWM, it is always custom-made,” Stefan Fink explains.
Schoeller inspect and repair their own machines
Some Schoeller employees attended training at the EWM headquarters in Mündersbach to equip them with the skills to independently carry out machine inspections. In the past, Schoeller would either send the machines in or an EWM field sales employee would visit their factory. But now, with 300 machines in operation, it is more efficient for the company to task their own employees with this, so Schoeller now carries out annual safety tests on the welding machines. The company uses the portable calibration and validation device from EWM, which it purchased specifically for this purpose. “We work with a maintenance tool that tells us when a given machine needs to be inspected. The standard test takes no more than 15 minutes, so it can be completed quickly as long as no anomalies are identified in the machine,” Stefan Fink explains. In the rare cases where an anomaly is found, Schoeller can count on the service of EWM. If a machine needs to undergo maintenance, Schoeller can make use of one of the replacement machines from EWM.
EWM machines overcome special challenges
In addition to the rapid replacement of the machines within its own systems, Schoeller has had special demands of EWM welding machines for many years. They need to be interface-compatible and able to withstand heavy workloads in continuous operation, have a high current stability and be flexible for use on new and old systems. Because EWM machines are so compact, Schoeller can integrate them into the production line close to where they are intended for use. Stefan Fink ends with a positive conclusion: “Our collaboration with EWM is going excellently. Their skilled employees work with us to find solutions, even at short notice. Thanks to our long-standing relationship of trust, I have contacts at EWM who I know so well that it’s almost as if we went to school together.”
Stand: 05 November 2019
Umfang: 7,155 characters including spaces
Abbildungen: 4