Nachhaltig schweißen
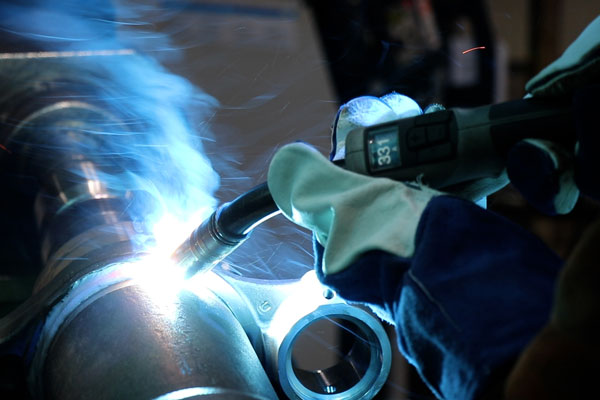
Nachhaltig schweißen
Wie sich Ressourcen schonen und gleichzeitig Kosten einsparen lassen
Nachhaltigkeit und Klimaschutz gewinnen in Industrieunternehmen immer mehr an Bedeutung. Dabei ist eine nachhaltige Produktion nicht zwangsläufig mit einer Kostensteigerung verbunden. Mit der Initiative BlueEvolution® zeigt EWM, wie sich Wirtschaftlichkeit und Ökologie beim Schweißen in Einklang bringen lassen. Eine rohstoffsparende Invertertechnologie und energiereduzierende Fügeverfahren verbessern nicht nur die Ökobilanz, sondern steigern auch die Effizienz der Schweißprozesse deutlich.
Um nachhaltig zu produzieren, müssen Unternehmen soziale, ökologische und ökonomische Belange in ein vernünftiges Verhältnis zueinander stellen. Das gilt auch für Schweißprozesse. Dabei lässt sich an vielen Stellschrauben drehen, wenn sowohl die Herstellung und Verwendung der Geräte als auch die Durchführung der Prozesse unter umweltfreundlichen Aspekten erfolgen soll. So führt beispielsweise der Einsatz von Invertertechnik zu einer deutlichen Rohstoffeinsparung bei gleichzeitiger Steigerung der Effizienz. Stromquellen auf Transduktor- oder Magnetverstärkerbasis sowie weitere Geräte mit Primärtransformator haben größere Energieverluste als moderne Inverter, die mit einem hohen Wirkungsgrad punkten und weniger Energie benötigen. Eine von EWM durchgeführte Untersuchung zeigt, dass sich der Stromverbrauch beim Einsatz der Phoenix XQ 400 mit Invertertechnologie im Vergleich zur stufengeschalteten Stromquelle WEGA 400 um 3.643 kWh im Jahr reduziert. Das gilt für das Schweißen im Bereich des Sprühlichtbogens mit einem Zusatzdraht mit Durchmesser von 1,2 mm. Die Stromkosten sinken unter Berücksichtigung der Energiepreise zum Zeitpunkt der Messung um circa 730 Euro. Inverter sind nicht nur effizienter, sondern auch um ein Vielfaches kompakter und leichter als stufengeschaltete Stromquellen. So wiegt beispielsweise der Transformator eines stufengeschalteten Schweißgerätes mit einer Leistung von 20 kW circa 100 kg. Dagegen hat der Transformator der Titan XQ 350 puls von EWM mit der gleichen Leistung nur ein Gewicht von 5 kg. Für die Herstellung der Inverter-Stromquellen wird somit auch weniger Material benötigt und dementsprechend eine geringere Menge Kupfer, Aluminium und Stahl verbraucht. Darüber hinaus sorgt der Einsatz von Inverter-Stromquellen für eine Reduzierung der CO2-Emissionen. Das zeigt sich schon bei der Herstellung. So fallen beim Bau von 10.000 Inverter-Stromquellen pro Jahr über 1.100 t weniger CO2 an als beim Bau von Stromquellen konventioneller Technik.
Vorteile der Invertertechnologie
Bei dem Einsatz von stufengeschalteten Schweißgeräten kann der Anwender kaum Einfluss auf die Regelung der Schweißprozesse nehmen. Mit der Inverter-Stromquelle dagegen lassen sich wellenformgesteuerte Schweißprozesse realisieren, die Energiekosten und Schweißrauchemissionen erheblich reduzieren. So ermöglichen beispielsweise die Schweißprozesse forceArc® XQ und forceArc® puls XQ von EWM deutlich kleinere Nahtöffnungswinkel im Vergleich zu herkömmlichen Schweißprozessen. Damit müssen weniger Raupen geschweißt werden. Das reduzierte Schweißnahtvolumen hat Auswirkungen auf Schweißvorbereitungszeiten und Schweißzeiten. Die wärmeminimierten, richtungsstabilen und druckvollen Lichtbogen mit tiefem Einbrand im oberen Leistungsbereich ermöglichen darüber hinaus eine Reduzierung von Schweißzusatzwerkstoffen. Aufgrund des geringen Spritzeraufkommens ist zudem weniger Nacharbeit erforderlich. Im Ergebnis profitieren Anwender von einer Einsparung von Energie, Material, Zeit und Kosten. Im Vergleich zu herkömmlichen Schweißgeräten mit einem Standard-Sprühlichtbogen lassen sich mit forceArc® XQ sogar bis zu 60 % Gesamtkosten einsparen.
Emissionen signifikant verringern
Wärmereduzierende Prozesse wie forceArc®, forceArc puls® und coldArc® reduzieren die Emissionen schädlicher Schweißrauchpartikel, wodurch Mensch und Umwelt geschützt werden. „Die Technische Universität Dresden hat in einer Studie belegt, dass die Emissionen mit dem Einsatz von forceArc® im Vergleich zum Schweißen mit einem herkömmlichen Sprühlichtbogen um bis zu 40 % reduziert werden können“, sagt Dipl.-Wirtsch.-Ing. Boyan Ivanov, Technischer Vertriebsleiter bei EWM. „Es entsteht ein höherer Schweißrauchniederschlag auf der Werkstückoberfläche, weshalb diese Emissionen nicht in die Umgebung freigesetzt werden. Somit sorgt das Verfahren für verbesserte Arbeits- und Umweltbedingungen.“ In einer weiteren Studie der RWTH Aachen wurde die Wirkung des forceArc®-puls-XQ-Prozesses bestätigt. Beim Schweißen von hochlegierten CrNi Stählen sank die Emissionsrate bei einer Drahtvorschubgeschwindigkeit von 13 m/min um das 4,5-Fache, verglichen mit einem Schweißprozess mit herkömmlichem Impulslichtbogen. Vor allem bei höheren Leistungen werden die Vorteile des forceArc®-puls-XQ-Prozesses deutlich. Auch der coldArc®-Prozess führt im Vergleich zum Standard-Schweißverfahren mit Kurzlichtbogen zu deutlich geringeren Emissionswerten. Grundsätzlich entsteht viel Schweißrauch, wenn der Schweißzusatzwerkstoff das Werkstück berührt und es zum Kurzschluss kommt. „Die Kurzschlussauflösung können wir sehr gut mit dem Inverter kontrollieren“, so Boyan Ivanov. „Der Kurzschluss erfolgt dann kontrolliert und der Schweißrauch wird minimiert. Auch entstehen dabei kaum Spritzer.
Den Gasverbrauch langfristig reduzieren und Prozesse sichern
Häufig wird die Gasmenge im Schweißprozess nicht korrekt eingestellt, sondern überdimensioniert. Die Folge sind erhöhte Gaskosten sowie Qualitätsverluste bei der Schweißnaht. Es bilden sich Poren, die zu porösen Schweißnähten führen können, oder Spritzer, die anschließend in zeitraubender und kostenintensiver Nacharbeit wieder entfernt werden müssen. Mit der elektronischen Gasmengenregelung im Drahtvorschubgerät lässt sich dies vermeiden. Aufgrund der elektronischen Regelung ergibt sich ein konstanter Gasdurchfluss. Das Schutzgas lässt sich aktiv regeln. Ändert sich etwas in der Gaszuführung, passt das Gerät die Menge automatisch an und sendet gegebenenfalls eine Fehlermeldung, wenn die zuvor angegebenen Grenzen über- oder unterschritten werden. Somit wird zum einen ein stabiler und sicherer Prozess gewährleistet und zum anderen ein unnötig hoher Gasverbrauch verhindert. Aufgrund des sanften Öffnens und Schließens des elektrischen Ventils entstehen keine Verwirbelungen beim Zünden des Lichtbogens. Die laminare Gasführung der EWM-Brenner sorgt für eine Reduzierung des Schutzgases um bis zu 25 %.
Energieverbrauch und CO2-Emissionswerte immer im Blick
Nachhaltig schweißen bedeutet aber auch, dass der gesamte Prozess überprüft und überwacht werden muss. Sollen Verbesserungen in puncto Umweltschutz erzielt werden, muss zunächst einmal bekannt sein, wie hoch der Ressourcen- und Energieverbrauch überhaupt ist. Mit dem Welding-4.0-Schweißmanagement-System EWM Xnet lässt sich dies leicht feststellen. Alle Schweißgeräte im Werk werden miteinander vernetzt. Schweißdaten, Verbrauch und Kosten lassen sich so für unterschiedliche Bauteile aufzeigen und verwalten. Die Verbrauchswerte hinsichtlich Gas, Energie und Werkstoff werden kontinuierlich aufgezeichnet. So lassen sich Einsparpotenziale direkt identifizieren. Rechtzeitig wird auf notwendige Wartungen hingewiesen, um die Lebensdauer der Anlagen und Geräte zu optimieren. Im Ergebnis sichert das System die Qualität, ermöglicht Prozessverbesserungen und vereinfacht die Dokumentation. „Xnet berechnet für jedes Schweißgerät den Energieverbrauch – pro Tag oder pro Auftrag, je nach Bedarf“, erklärt Boyan Ivanov. „Mit unserer neuen Version ermöglichen wir gleichzeitig eine Kalkulation der Emissionswerte. So lässt sich leicht feststellen, ob die CO2-Emissionen im festgelegten Rahmen oder zu hoch sind und dementsprechend verringert werden müssen.“ Mit EWM Xnet verfügt das Unternehmen somit über ein wichtiges Kontrollwerkzeug in einem Markt, in dem die Menge an CO2-Zertifikaten ständig weiter sinkt und die Preise für die Zertifikate steigen. Denn die Regeln für den EU-Emissionshandel werden schon jetzt verschärft, um die Treibhausgas-Produzenten dazu zu bewegen, dass sie weitere Maßnahmen für den Klimaschutz umsetzen. Die CO2-Zertifikate sind ein wichtiger Teil der Gesamtbilanz von Unternehmen. Mit der Schweißmanagement-Software liefert EWM einen bedeutenden Baustein, um die Qualität der Schweißprozesse zu verbessern, die Kosten und Emissionen zu senken und letztlich die Produktivität in Verbindung mit einer Steigerung der Nachhaltigkeit zu erhöhen.
Fazit: Nachhaltig schweißen rechnet sich
„Wir sind als einer der ersten Schweißgerätehersteller mit unserer Nachhaltigkeitsinitiative BlueEvolution gestartet“, konstatiert Boyan Ivanov. „Damit zeigen wir, dass dank moderner Technik und innovativen Schweißprozessen weniger Rohstoffe verbraucht und Energie aufgewendet werden muss, was zu Klimaschutz und Nachhaltigkeit beiträgt und sich gleichzeitig in sinkenden Kosten bemerkbar macht.“ Schweißzeiten können verkürzt werden, wodurch die Produktivität steigt. Zusätzlich lassen sich erhebliche Mengen an Emissionen reduzieren, was nicht nur die Ökobilanz, sondern auch die Arbeitsplatzbedingungen verbessert. Dabei unterstützt die EWM-Technologie auch zukunftsgerichtete Konstruktionen und den Einsatz neuer Materialien. So geht beispielsweise der Trend im Kranbau, aber auch im Bau von Windenergieanlagen zum Einsatz dünner und gleichzeitig extrem fester Materialien. Damit diese sensiblen Werkstoffe optimal verschweißt werden können, bedarf es speziell darauf ausgerichteter Verfahren und entsprechender Invertertechnologie sowie einer umfangreichen Expertise. Und auch für diesen Einsatzbereich gilt: Eine Schweißnaht ist für EWM erst dann perfekt, wenn dabei Energie und Ressourcen geschont werden.