EWM welding machines already comply with EU Directive
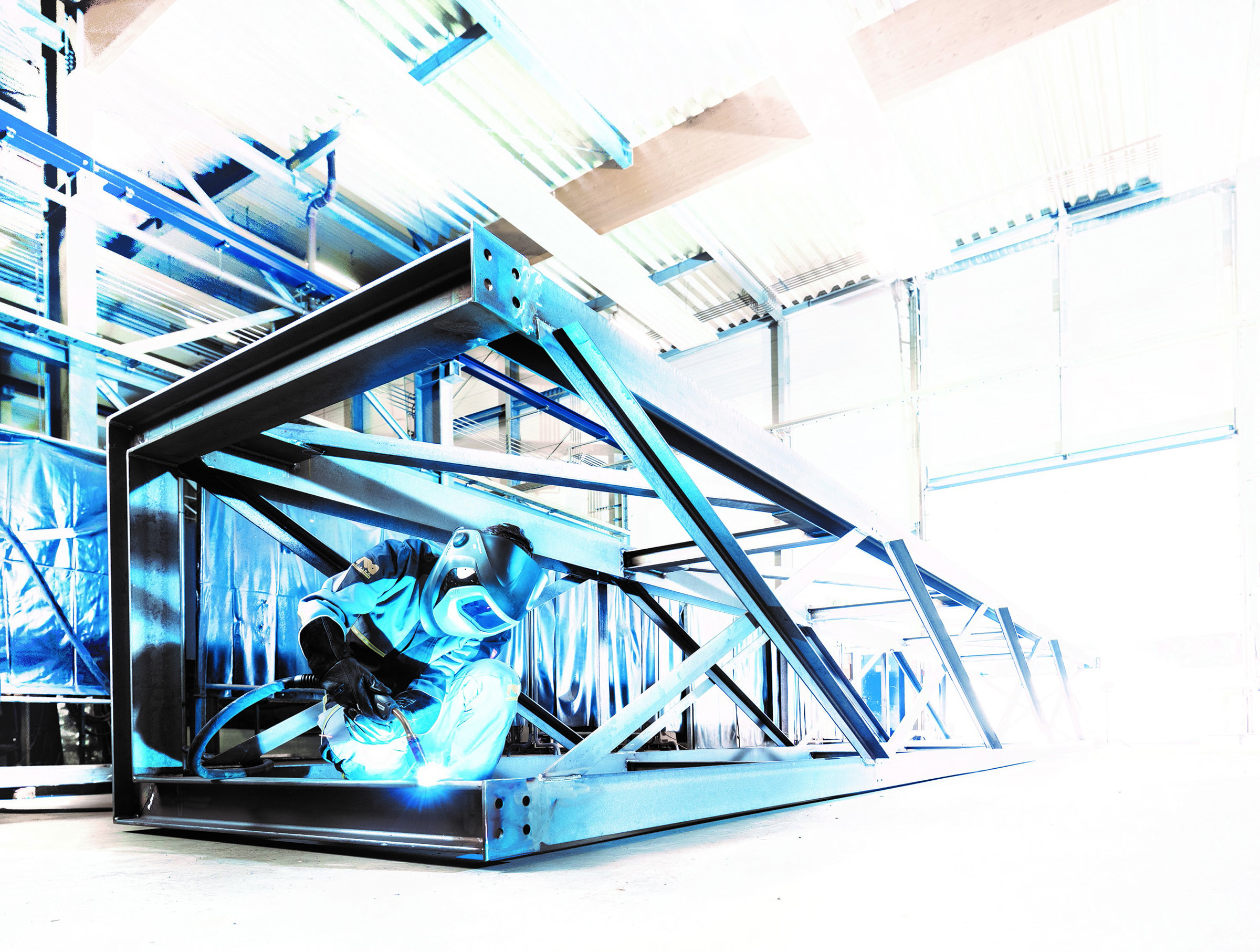
EWM welding machines already comply with EU Directive
EWM Taurus Steel saves electricity and costs
With welding machines from the Taurus Steel series, EWM AG customers are already meeting the requirements of the EU Ecodesign Directive. These MIG/MAG welding machines by EWM, Germany’s leading manufacturer of arc welding technology and one of the world’s leaders in technology, have been designed for working with steel. Thanks to state-of-the-art inverter technology, the machines are resource-efficient and, true to EWM quality, extremely durable and powerful, saving companies real money. This makes welding machines from the Taurus Steel series a veritable alternative to step switch-controlled machines:
Comparison calculations show that through the low power consumption alone, companies using an EWM Taurus Steel machine save more than 3000 kWh per year in comparison to a step switch-controlled welding machine. That translates to almost two tonnes less CO2 and, with an electricity price of 20 cents per kWh, around 600 euros worth of cost savings a year – and that’s just one, single machine. For steel and metal-working industries and shipyards, as well as for steel construction companies, there is huge potential for savings with initial procurement costs being paid off in no time.
Thanks to their large power reserves and renowned EWM quality, machines in the Taurus Steel series are suitable for continuous use in three-shift operation. It’s not for nothing that the premium welding machine manufacturer offers a three-year guarantee on machines and a five-year guarantee on transformers and chokes, all without a limitation on operating hours.
The machine controls are easy to operate and the welding task can be quickly set up with 100% reproducibility. EWM now offers the Taurus Steel in three power variants. In addition to the Taurus Steel 400 A and 500 A models, EWM now also offers the brand-new Taurus Steel 355 with 350 A output. All three products have an incredible duty cycle. The 350 and 500 variants boast a duty cycle of 60% at maximum current, while the 400 variant offers a 100% duty cycle for easy welding with full penetration. This is all down to state-of-the-art EWM inverter technology that saves electricity while significantly reducing the weight.
The Taurus Steel Synergic is an inverter welding machine with a synergic control concept and optimised characteristics for steel. Thanks to the synergic function, parameters adapt automatically to the specified settings. The inverter-pulse welding machine, the Taurus Steel puls, also offers an additional, convenient pulse function. This ensures less weld spatter, reducing the need for finishing work. Last but not least, the Taurus Basic S is an inverter welding machine with non-synergic twin-knob operation, perfect for the more traditional welders out there.
With their modular system and associated wire feeders, the Taurus Steel machines are incredibly flexible and – depending on the assembly of intermediate hose packages and welding torches – also have a large working radius. The EWM welding machines are robust and perfect for use in demanding work environments. This makes all three variants perfect alternatives to the step switch-controlled welding machines still widely used throughout Germany. Their power sources are significantly lighter than machines with transformers and they are easy to transport thanks to their modular casing. The water block is also quick and easy to dismantle, making the Taurus Steel easy to transport in a car boot, for example.
With EWM already meeting the requirements of the new EU Ecodesign Directive, by purchasing one of each machine, EWM customers are also ready for the future. From 1 January 2021, the Directive will ensure that consumers can more easily repair large electrical equipment. From 2023, welding machines in open circuit and during the welding process must not use more than 50 kWh each. The aim is to save 167 terawatt hours (TWh) of energy per year by 2030 – as much as is currently consumed by the entire country of Denmark in one year.
Date: 03 April 2020
Volume: 4,123 characters including spaces
Figures: 3