ISW Steel Components relies on EWM welding equipment
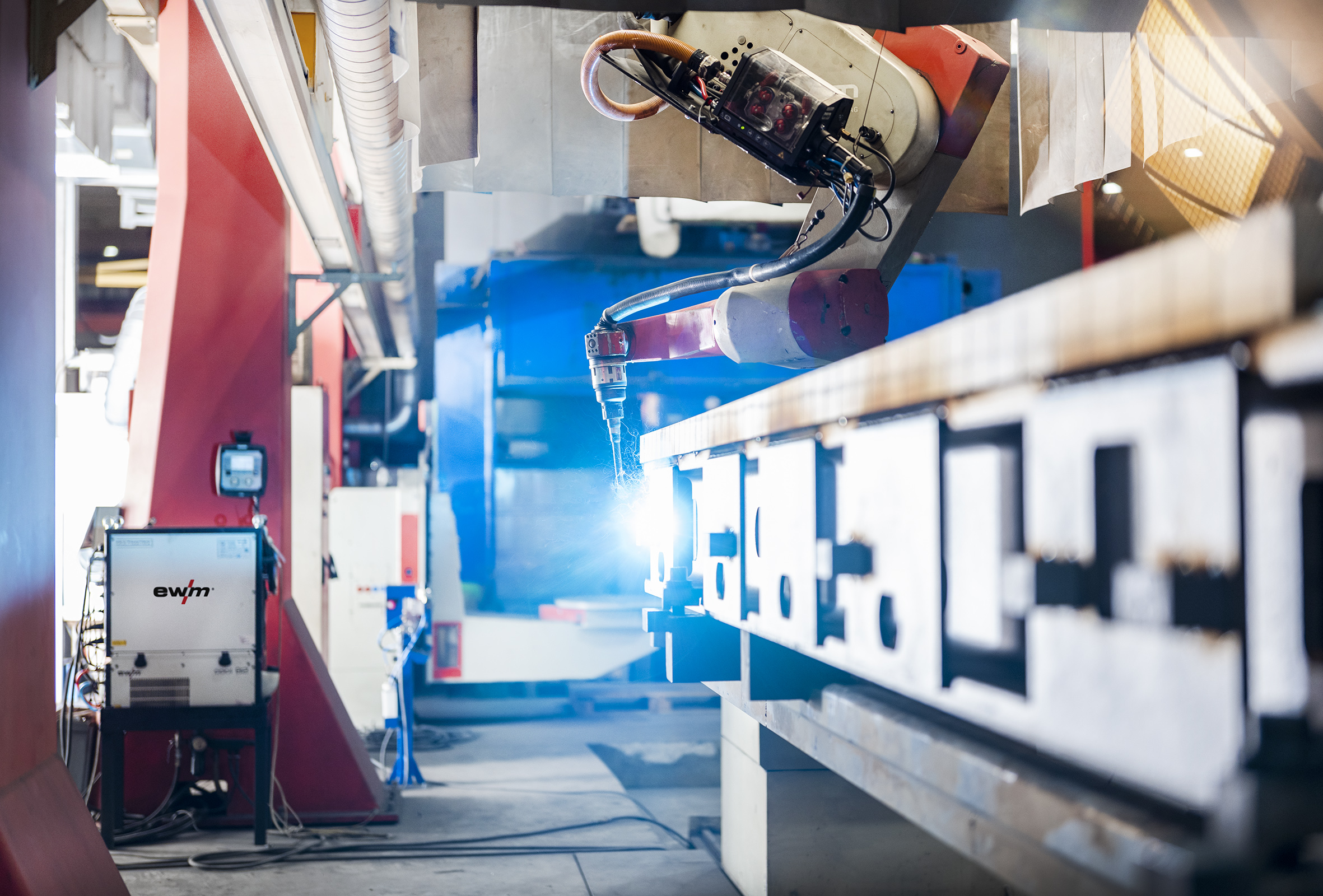
ISW Steel Components relies on EWM welding equipment
Eight hours, 350 amperes, one EWM contact tip
Black steel with a thickness of 300 millimetres and over, lengths of up to 20 metres and a total weight of up to 100 tonnes: these dimensions are the speciality of ISW GmbH Steel Components from Ennsdorf in Lower Austria. The contract manufacturer specialises in producing large, heavy and complex basic frames for machines and systems. The weld seams are mainly carried out using the MAG welding procedure with high levels of current and multi-layer welding. This is a real test for the welding torch contact tip, which is responsible for the quality of the weld seams among other things. As their customers need comprehensive quality assurance and traceability, ISW relies on EWM welding technology from welding machines to welding processes and quality assurance using ewm Xnet 2.0, right through to welding torches and contact tips.
Even though it is one of the smallest components in a welding machine, the contact tip is crucial to the process. It doesn’t just conduct the welding current of 350 amperes and more to the electrode, but also guides this filler wire to the welding spot. In 2008, the company switched all its welding production over to EWM products: the welders tested machines from three major manufacturers and decided on the machines from the Westerwald welding machine manufacturer.
Existing automation solutions have been retrofitted over the past few years. The robotic welding system was equipped with a new power source – an alpha Q from EWM. It is equipped with Titan technology with all the innovative EWM welding processes and new EWM welding torches for automated use. Plus, the system was also connected to ewm Xnet 2.0.
Only EWM contact tips have been used for automated manufacturing since then. EWM contact tips are made from high-quality CuCrZr and have a 15 per cent longer contacting surface compared to the M8 standard contact tip, as well as a 30 per cent larger threaded cross section. The contact with the welding wire is better and heat is dissipated more effectively.
A contact tip is in a welding torch for up to eight hours. This is the average length of time it takes to weld a component in the automated system. As a result, throughput times could be increased. Previously, contact tips only lasted a maximum of one hour. Now, an entire component can be finished with EWM. “The tip can probably last longer, but we prefer to err on the side of caution,” said Stefan Limberger, Managing Director of ISW. “And this is even though we use high currents of 350 amperes and more.”
Functionalities of the welding torch
A particular advantage according to ISW is that the same contact tips are used for both the MT or, as of late, the PM series of EWM welding torches when welding manually. The downtime during manual manufacturing is also significantly reduced thanks to the longer service life of the consumables. This improves productivity. However, there is also another feature of the welding torch that is particularly advantageous for welders: no need to walk back and forth. Thanks to the integrated control and graphic display on the RD3X professional welding torch, the relevant parameters can be set directly on the welding torch. Thus, reducing the need to walk a long way back to the welding machine. This is particularly useful for welders when working on large components or in hard-to-reach places. They can adjust the parameters without leaving their position. The LED lighting on the welding torch lights up dark working areas and the ergonomic and convenient design, as well as the balance and weight of the welding torch are other features that make work significantly easier for welders.
Less heat and less distortion thanks to forceArc puls
“After 10 years it was time to invest in welding technology again and bring our machines up-to-date,” said Stefan Limberger about the procurement of Phoenix and Titan XQ puls welding machines. Welding technology has developed significantly over the past few years. In addition to the new welding torches, the innovative forceArc puls welding process was of particular interest to ISW welders and is now the sole welding process used for manufacturing. This powerful arc is characterised by good penetration while simultaneously reducing heat input significantly. This is particularly important for multi-layer welding. Less heat input means less distortion and less tension in the component and thus less arduous straightening work. Forces of up to 600 tonnes are in action here. Finishing work is also reduced to a minimum as the welding is mostly spatter-free. This welding process also increases welding speed – a welcome side-effect.
Continuous welding data collection for quality assurance
In addition to the innovative welding process, the new machines continuously collect welding data in real time. Based on this data, the ewm Xnet 2.0 quality management software can analyse and manage all welding processes with network support. This provides quality assurance for the welding processes but also aids productivity in the workplace. As a pure contract manufacturer, ISW places particular importance on providing their customers with seamless and comprehensive quality assurance. “With Xnet, I can use hard facts to prove that we have welded to the parameters specified and that they weren’t just defined beforehand in the WPS,” emphasised Stefan Limberger.
ISW uses this type of data collection for all their welding tasks, in particular for automated processes. All the welding-relevant data for the large components is collected. The data collected is transferred to a server via an external gateway attached to the machine using WiFi. Welding coordination personnel can access and view current welding data in real time if necessary. The data is not lost even if the data connection between the gateway and server is lost. It is stored temporarily and then transferred when the connection is re-established.
Increased productivity due to data analysis
ISW doesn’t just use data collection and analysis for quality assurance, but also for increasing productivity because the welding coordinators can now analyse the off and on times of the welding machines. This way, they discovered long breaks in welding when the welders had to retrieve and position materials during a manufacturing process. By using a manipulator, these non-productive times were reduced so much that the same output can now be achieved in just three shifts instead of four.
Stefan Limberger is convinced that continuous and electronic data collection will be implemented more and more in the welding industry. This is already state-of-the-art in the high-quality sector and is a prerequisite of customers. Does he recommend the ewm Xnet 2.0 software? “Definitely – as long as you aren’t our competitors.”
Date: 25. August 2020
Volume: 6,779 characters including spaces
Images: 7 (for download)