ISW Steel Components setzt auf die Schweißausrüstung von EWM
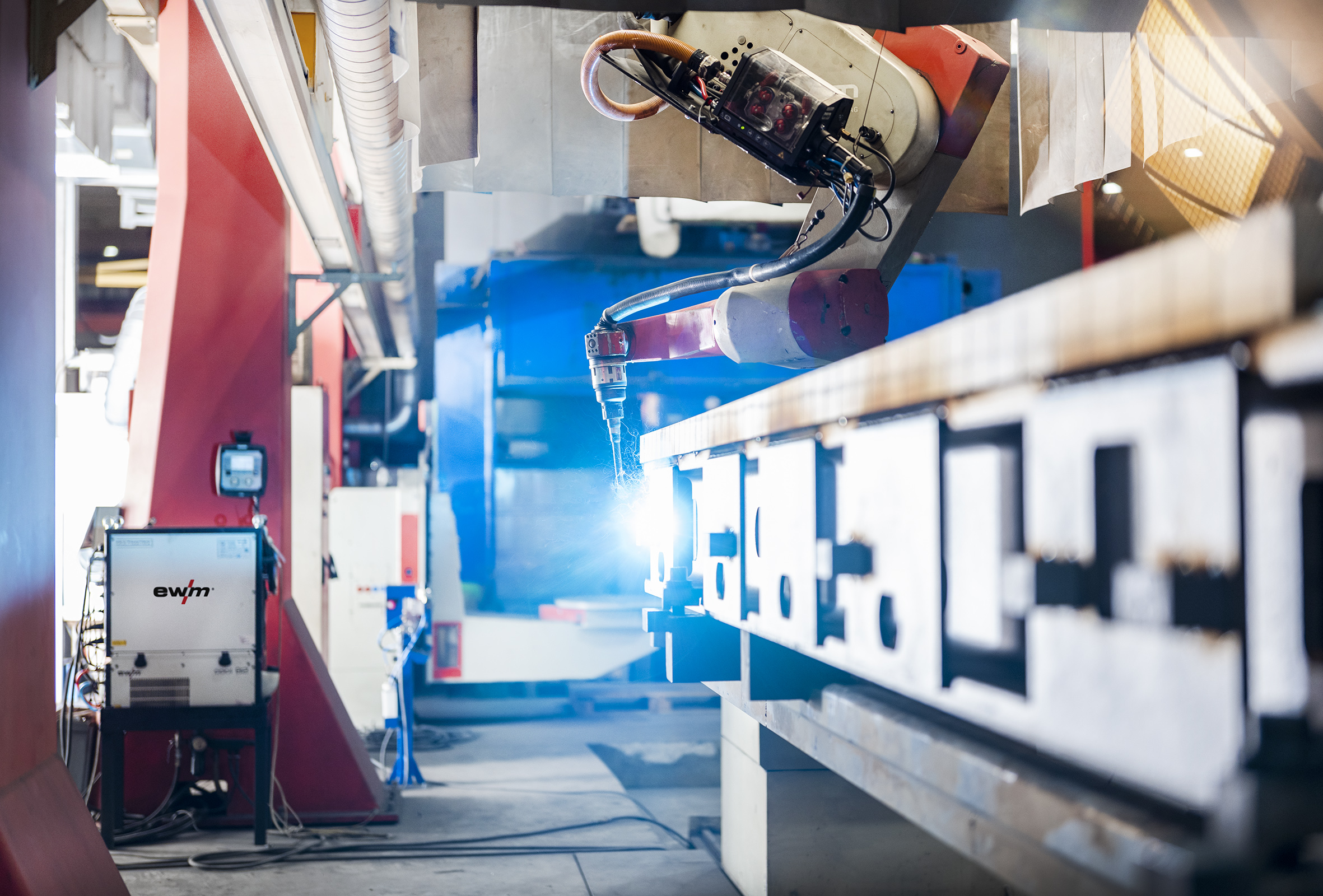
ISW Steel Components setzt auf die Schweißausrüstung von EWM
8 Stunden, 350 Ampere, 1 EWM-Stromdüse
Schwarzstahl mit einer Dicke von 300 Millimetern und mehr, Längen von bis zu 20 Metern und ein Gesamtgewicht von bis zu 100 Tonnen: In diesen Dimensionen ist die ISW GmbH Steel Components aus dem niederösterreichischen Ennsdorf zuhause. Der Lohnfertiger hat sich auf die Herstellung großer, schwerer und komplexer Grundrahmen für Maschinen und Anlagen spezialisiert. Die Schweißnähte werden hauptsächlich im MAG-Schweißverfahren mit hohen Strömen und als Mehrlagenschweißungen ausgeführt. Das ist eine echte Anforderung an die Stromdüse des Schweißbrenners, die neben anderem für die Qualität der Schweißnähte mitverantwortlich ist. Da die Kunden eine umfassende Qualitätssicherung und Rückverfolgbarkeit fordern, setzt ISW auf die Schweißtechnik von EWM – von den Schweißgeräten über die Schweißprozesse und die Qualitätssicherung mit ewm Xnet 2.0 bis hin zu den Schweißbrennern und den Stromdüsen.
Auch wenn es eines der kleinsten Bauteile ist, so ist die Stromdüse doch mit prozessentscheidend: Sie leitet nicht nur den Schweißstrom von 350 Ampere und mehr in die Drahtelektrode ein, sondern führt diesen Zusatzwerkstoff auch zum Schweißpunkt. 2008 stellte das Unternehmen seine Schweißproduktion komplett auf EWM um: Die Schweißer hatten sich nach einer Testphase mit den Geräten dreier namhafter Hersteller für die Geräte des Schweißgeräteherstellers aus dem Westerwald ausgesprochen.
In den vergangenen Jahren wurde an der bestehenden Automatisierungslösung ein so genanntes Retrofitting durchgeführt. Die Roboterschweißanlage wurde mit einer neuen Stromquelle, einer alpha Q von EWM, ausgestattet. Neben der darin enthaltenen Titan-Technologie mit allen innovativen EWM-Schweißprozessen und neuen Schweißbrennern von EWM für die automatisierte Anwendung erhielt die Anlage die Anbindung an ewm Xnet 2.0.
Seitdem kommen in der automatisierten Fertigung nur noch Stromdüsen von EWM zum Einsatz. Die EWM-Stromdüsen bestehen aus hochwertigem CuCrZr, haben eine 15 Prozent längere Kontaktfläche im Vergleich zur M8-Standardstromdüse und einen 30 Prozent größeren Gewindequerschnitt. Die Kontaktierung des Schweißdrahtes ist besser und die Wärme wird effektiver abgeleitet.
Bis zu acht Stunden Schweißzeit befindet sich eine Stromdüse im Brenner. So lange dauert es im Durchschnitt, bis ein Bauteil auf der automatisierten Anlage fertiggeschweißt ist. Dadurch konnten die Durchlaufzeiten erhöht werden. Früher hielt die Stromdüse maximal eine Stunde. Mit EWM kann ein komplettes Bauteil gefertigt werden. „Die Düse würde wahrscheinlich noch länger halten, aber wir gehen da lieber auf Nummer sicher“, meint Stefan Limberger, Geschäftsführer von ISW. „Und das, obwohl wir die ganze Zeit über mit hohen Strömen von 350 Ampere und mehr schweißen.“
Funktionalitäten im Schweißbrenner
Beim manuellen Schweißen mit den EWM-Schweißbrennern der MT- oder neuerdings der PM-Baureihe kommen dieselben Stromdüsen zum Einsatz, was ISW als besonders vorteilhaft bewertet. Auch in der manuellen Fertigung werden die Stillstandzeiten durch die längere Lebensdauer des Verschleißteils deutlich reduziert. Das erhöht die Produktivität. Doch für die Schweißer ist noch ein anderer Aspekt an den Brennern von großem Wert: Es fallen viele Laufwege weg. Dank der integrierten Steuerung beim Profi-Schweißbrenner RD3X mit grafischer Anzeige lassen sich sämtliche relevanten Parameter direkt am Brenner einstellen. So kann der oft lange Weg zum Schweißgerät unterbleiben. Gerade bei der Arbeit an den großen Bauteilen oder in Zwangspositionen hilft das den Schweißern. Sie können die Parameter anpassen, ohne ihre eigene Position verändern zu müssen. Die LED-Beleuchtung am Schweißbrenner, die dunkle Arbeitsbereiche ausleuchtet, der ergonomische und handliche Aufbau sowie die Ausgewogenheit und das Gewicht des Brenners sind weitere Aspekte, die den Schweißern die Arbeit deutlich erleichtern.
Weniger Wärme und weniger Verzug durch forceArc puls
„Nach 10 Jahren war es an der Zeit, mal wieder in Richtung Schweißtechnik zu investieren und die Geräte auf den neuesten Stand zu bringen“, erklärt Stefan Limberger die Anschaffung von Phoenix- und Titan XQ puls-Schweißgeräten. In den vergangenen Jahren hatte sich im Bereich der Schweißtechnik erstaunlich viel getan. Neben den neuen Brennern war es insbesondere der innovative Schweißprozess forceArc puls, der auf besonderes Interesse bei den Schweißern von ISW stieß und inzwischen als einziger Schweißprozess in der Fertigung eingesetzt wird. Dieser druckvolle Lichtbogen zeichnet sich durch einen guten Einbrand bei gleichzeitig deutlich reduzierter Wärmeeinbringung aus. Das ist gerade beim Mehrlagenschweißen von besonderer Bedeutung. Geringere Wärmeeinbringung bedeutet weniger Verzug und weniger Spannungen im Bauteil und damit weniger mühselige Richtarbeit – Kräfte von bis zu 600 Tonnen kommen da zum Einsatz. Da die Schweißungen zudem weitgehend spritzerfrei erfolgen, ist auch die Nacharbeit auf ein Minimum reduziert. Dass sich mit diesem Schweißprozess zusätzlich die Schweißgeschwindigkeit erhöht, ist ein positiver Zusatzeffekt.
Kontinuierliche Schweißdatenerfassung zur Qualitätssicherung
Neben dem innovativen Schweißprozess bieten die neuen Geräte eine kontinuierliche Schweißdatenerfassung in Echtzeit. Anhand dieser Daten kann die Qualitätsmanagement-Software ewm Xnet 2.0 sämtliche Schweißprozesse netzwerkgestützt analysieren und verwalten. Das dient sowohl der Qualitätssicherung der Schweißprozesse als auch der Produktivität an den Arbeitsplätzen. Gerade als reiner Lohnfertiger ist es für ISW von besonderer Bedeutung, den Kunden die Qualität immer wieder lückenlos und umfassend belegen zu können. „Durch Xnet kann ich mit Hardfacts beweisen, dass wir mit den vorgegebenen Parametern geschweißt haben und sie nicht nur im Vorfeld über die WPS definiert wurden,“ betont Stefan Limberger.
ISW nutzt diese Art der Datenaufzeichnung bei allen Schweißaufgaben, insbesondere bei den automatisierten Prozessen. Sämtliche große Teile werden schweißtechnisch erfasst. Über ein externes Gateway, das an dem Gerät angebracht ist, werden die aufgezeichneten Daten per WLAN auf den Server übertragen. Bei Bedarf kann die Schweißaufsicht in Echtzeit auf die aktuellen Schweißdaten zugreifen und sich diese anschauen. Selbst wenn einmal die Datenverbindung zwischen Gateway und Server abreißt, bleiben die Daten erhalten. Sie werden zwischengespeichert und dann übertragen, wenn die Verbindung wieder aufgebaut ist.
Produktivitätssteigerung durch Datenanalyse
Neben der Qualitätssicherung nutzt ISW die Datenaufzeichnung und Datenanalyse auch zur Produktivitätssteigerung, indem die Schweißaufsichtspersonen die Einsatz- und Einschaltzeiten der Schweißgeräte analysieren. So waren in einem Fertigungsprozess plötzlich längere Schweißpausen aufgefallen, in denen die Schweißer Material holen und aufwendig richten mussten. Der Einsatz eines Manipulators konnte diese Nebenzeiten so weit reduzieren, dass die gleiche Leistung statt in vier nun in drei Schichten gefertigt werden kann.
Stefan Limberger ist überzeugt davon, dass sich die kontinuierliche und elektronische Schweißdatenerfassung in der Schweißbranche immer mehr durchsetzen wird. Im höherwertigen Bereich entspricht das bereits dem State of the Art und wird von den Kunden vorausgesetzt. Ob er diese Software ewm Xnet 2.0 weiterempfehlen kann? „Definitiv – wenn es nicht gerade ein Konkurrenzunternehmen ist.“
Stand: 25. August 2020
Umfang: 7.400 Zeichen inklusive Leerzeichen
Abbildung: 7 (unter Medien-Download)